Operations Optimization: How Conveyors Can Help You Go Lean
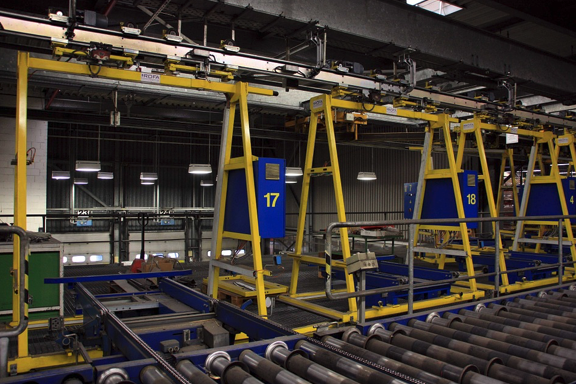
Conveyors are a great fit for lean environments. They automate processes, thereby improving work efficiency, and help reduce numerous types of process waste, both of which are quintessential to establishing lean practices within an operational setting.
Often, businesses planning to go lean shy away from using conveyors, as they believe the return on investment (ROI) for these equipment is quite low. However, that’s not true.
Conveyors, when applied correctly, can make big (and valuable) contributions to any lean environment.
Below, we take a look at some ways on how conveyors can help businesses go lean.
Conveyors help reduce unnecessary motion and enable proper utilization of workforce
In a lean environment, unnecessary motion and non-utilized talent are two of the main types of operational waste.
Motion refers to movement of staff or machinery performed during a process. An example can be warehouse labor manually carrying raw materials from one area of the factory floor to another area of the factory floor. Motion is a given in any operational setting, however, unnecessary motion should be avoided as it translates to the wastage of time and effort.
Non-utilized talent refers to the failure of management to ensure that all of its potential workforce is being efficiently utilized. It can be a by-product of many factors, including unnecessary motion, where employees are aimlessly moving inventory around the factory floor, when instead they could be performing value adding activities.
Conveyors help reduce unnecessary motion and enable efficient utilization of workforce by automating the conveying process. Using conveyors, inventory and products can be conveniently moved from one area of the factory floor to another without involving staff or load machines, thereby allowing proper and efficient utilization of available resources.
Conveyors help reduce processing errors and time
Processing errors and slow process times are also big hindrances to lean environments. Both increase operation costs and negatively impact customer experience.
When evaluating the leading factors that contribute to processing errors and slow process times, fatigue commonly stands out. Employees on the production line can get exhausted during the day while manually handling hundreds of thousands of loads. Consequently, their focus and speed suffer.
By automating the work flow, conveyors can help reduce employee fatigue, minimize processing errors and maximize process speed.
For instance, a conveyor can be used to orient products on an assembly line, ensuring the staff do not have to waste effort repositioning the product. Automatic sorting is another application area where conveyors can help reduce processing errors and maximize process speed.
All in all, conveyors serve as great solutions for lean environments and should be used by all businesses planning to go lean.
KD Equipment is one of the largest suppliers of storage solutions, material handling equipmentand loading dock door equipment and doors in the U.S. We supply high quality products at affordable price, including conveyors, pallet racks, modular offices, safety guards, dock door seals etc. Contact us to learn more about our product portfolio.
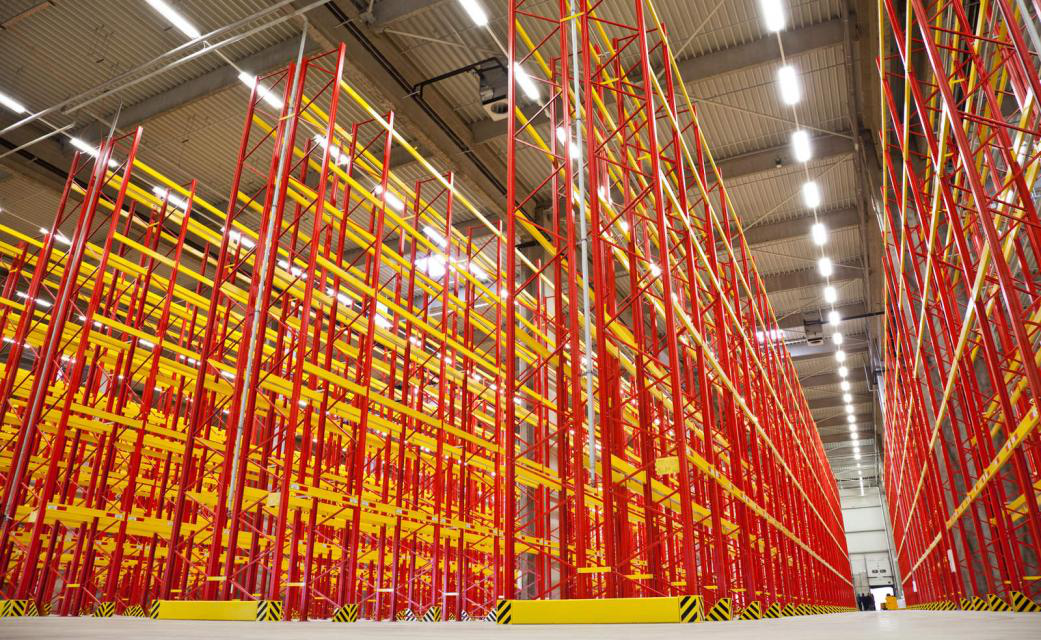
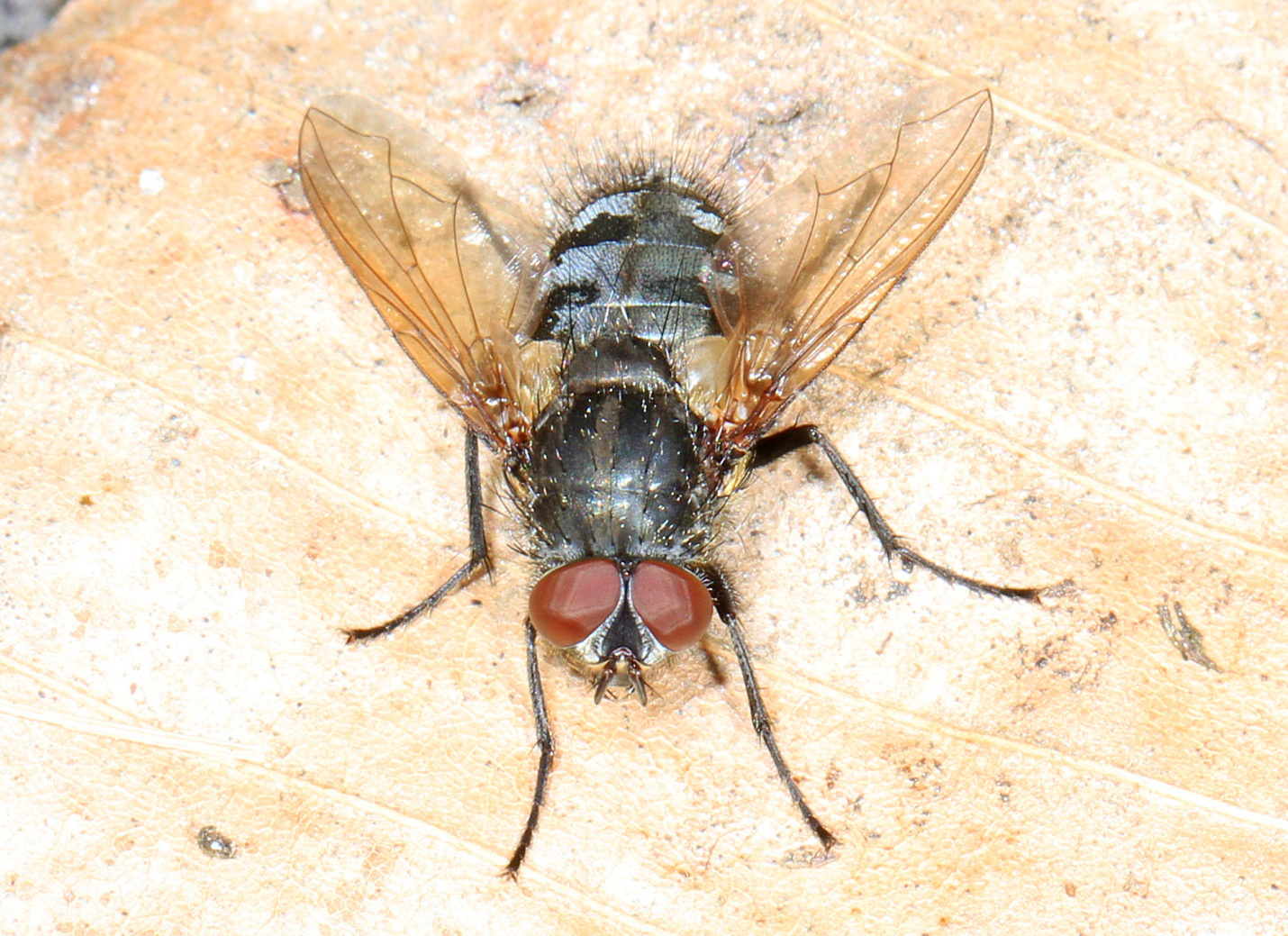
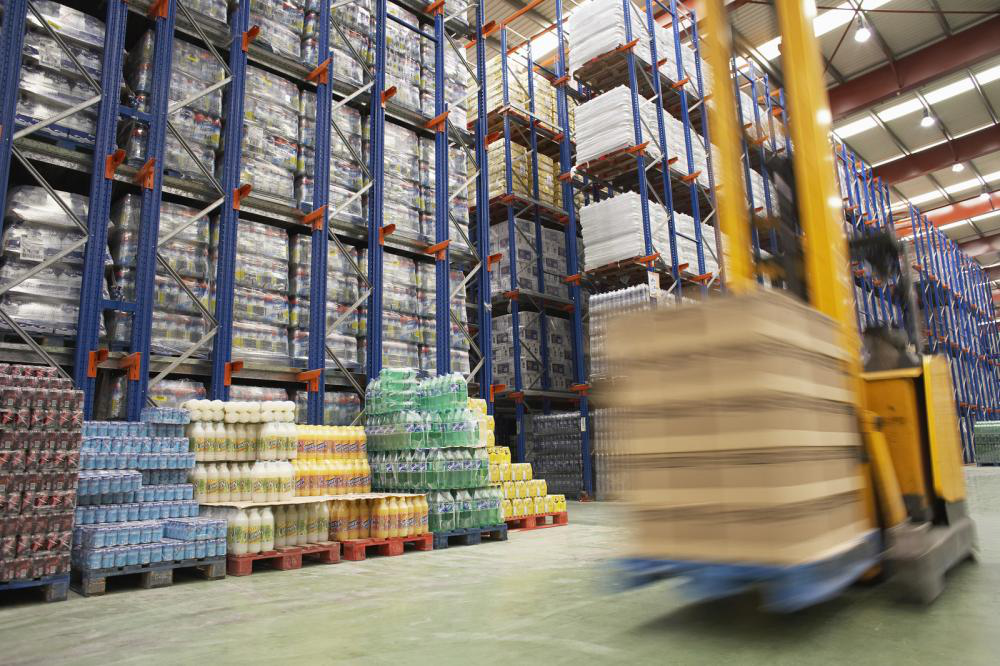
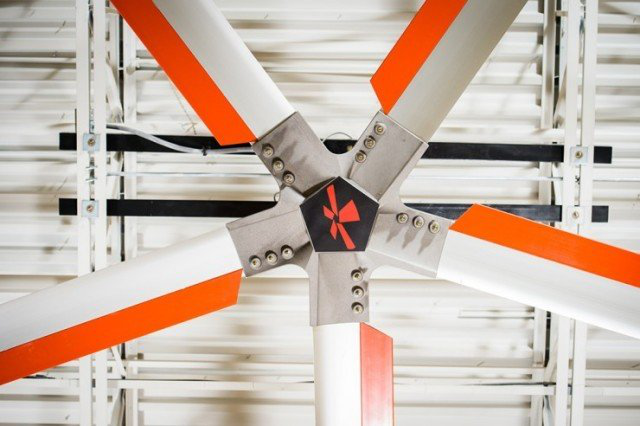
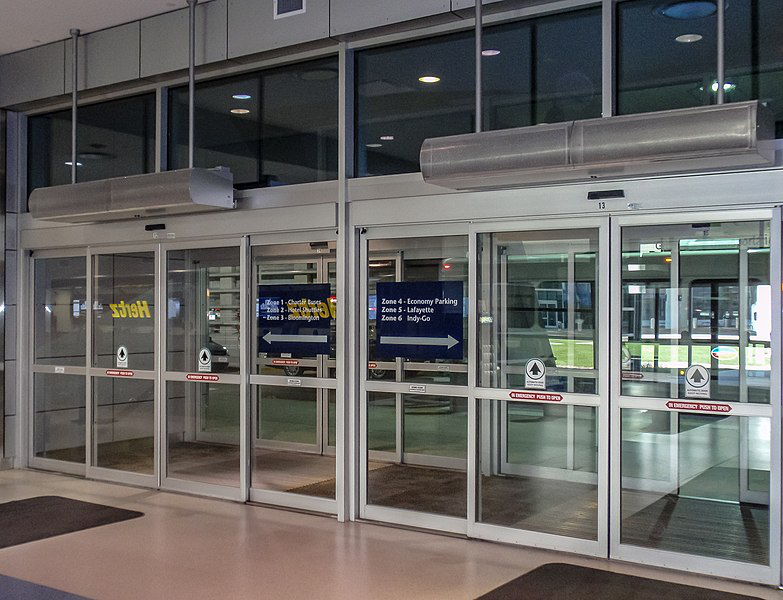
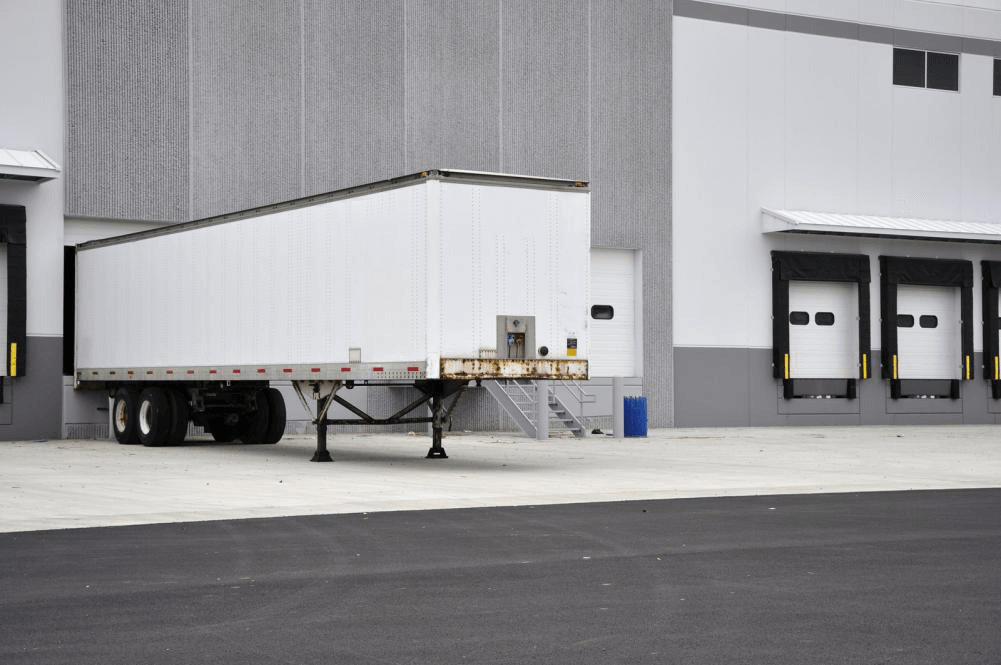
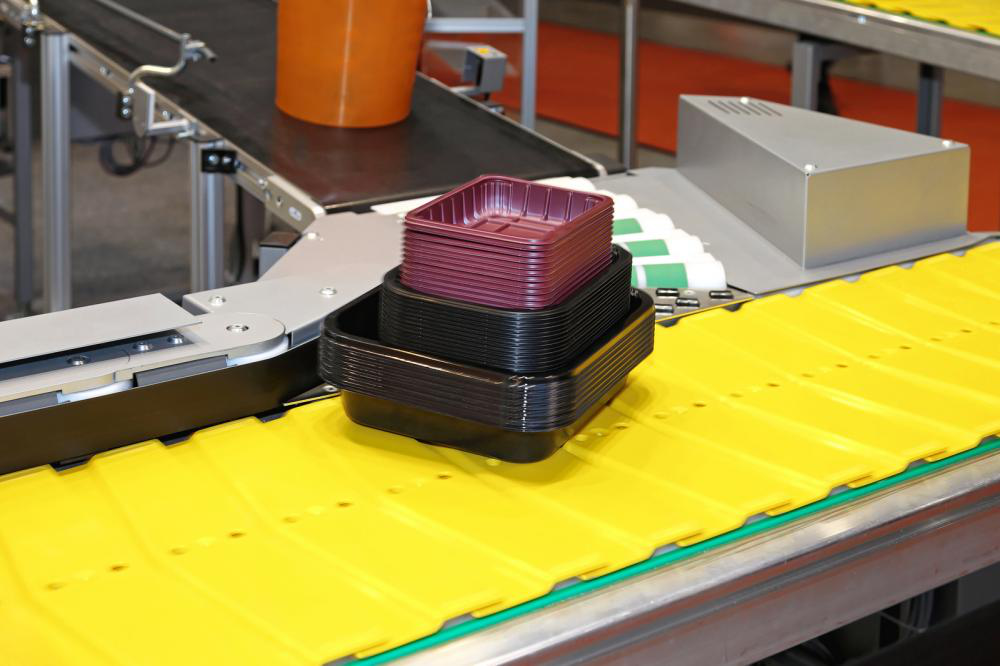
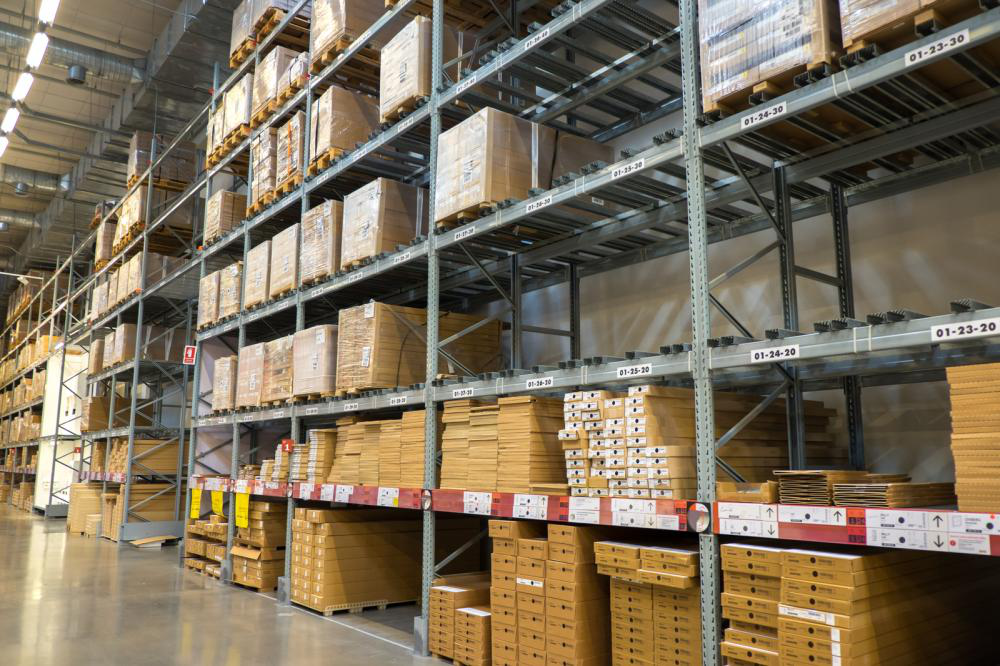
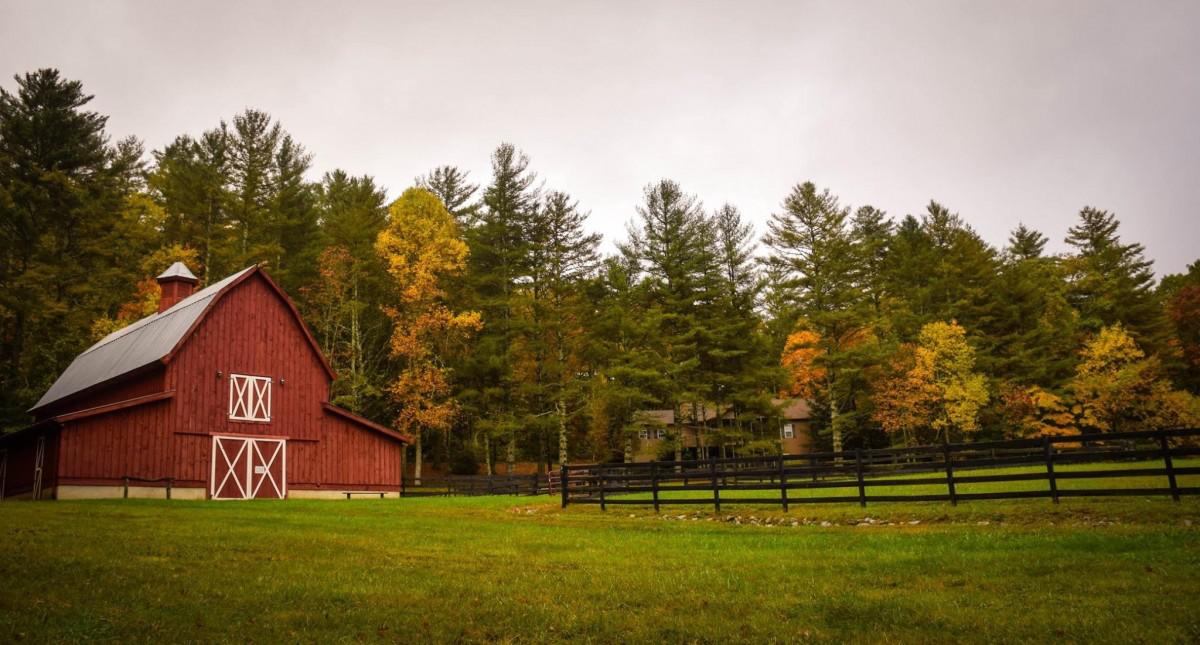
